洗涤塔注塑成型防回流:工艺***化与品质保障
在塑料加工***域,洗涤塔的注塑成型工艺要求严苛,而防止回流现象是确保产品质量与生产效率的关键要点。本文将深入剖析洗涤塔注塑成型中回流产生的原因、危害以及有效的防治策略,为相关生产实践提供全面且深入的参考。
一、洗涤塔注塑成型工艺概述
洗涤塔作为工业废气处理等场景的关键设备,其塑料部件通常采用注塑成型工艺制造。注塑成型是将颗粒状或粉状塑料原料注入模具型腔,经冷却固化获得所需形状制品的过程。在洗涤塔注塑成型中,原料多为耐腐蚀、耐化学性的塑料材料,如聚丙烯(PP)、聚氯乙烯(PVC)等,这些材料需在***的温度、压力和时间控制下完成注塑过程,以形成具有复杂结构的洗涤塔部件,如塔体、填料支撑等。
二、回流现象及其产生原因
(一)回流现象定义
在洗涤塔注塑成型过程中,回流是指已注入模具型腔的塑料熔体在保压或冷却阶段,由于某些因素导致熔体逆向流动的现象。这种回流可能破坏已形成的制品结构,造成表面缺陷、尺寸偏差甚至内部应力集中等问题,严重影响制品质量。
(二)产生原因
1. 模具方面
模具温度不均匀:模具不同部位的温度差异会导致塑料熔体在型腔内的冷却速度不一致。较热区域的熔体可能因周围熔体冷却收缩而产生回流。例如,在***型洗涤塔模具中,靠近浇口处若冷却不足,而远离浇口的部位冷却过快,就会形成温度梯度,诱发回流。
模具排气不***:模具内的空气在注塑过程中若不能顺利排出,会被压缩并形成阻力。当熔体压力稍有变化时,这些被困空气可能推动熔体回流。尤其在洗涤塔复杂的结构部件注塑时,狭小的缝隙和角落处更容易出现排气问题。
模具结构设计不合理:不合理的流道设计、浇口位置与数量不当等会使熔体在型腔内的流动不平稳。如浇口过小或位置偏移,可能导致熔体喷射进入型腔后产生紊流,在后续保压过程中引发回流。
2. 注塑机参数设置
注射压力与保压压力失衡:注射压力过高会使熔体过度充模,当保压阶段压力骤降时,熔体可能因压力差过***而回流。相反,保压压力不足则无法维持熔体对型腔的填充,也容易导致回流。在洗涤塔注塑中,由于制品壁厚可能不均匀,对压力的精准控制要求更高。
注射速度不恰当:注射速度过快,熔体冲击模具型腔壁后会产生较***的反作用力,可能引起熔体回流。而注射速度过慢,熔体在充模过程中容易冷却,同样会增加回流风险。
熔体温度波动:熔体温度过高,塑料分子运动剧烈,流动性过强,在保压和冷却过程中难以稳定成型,易出现回流。温度过低则会使熔体粘度增***,充模不完全,后续也可能因补料而产生回流。
3. 塑料原料***性
原料流动性差异:不同品牌、型号的塑料原料流动性不同。流动性差的原料在注塑过程中可能无法充分填满型腔,在保压阶段需要更多压力补充,从而增加了回流的可能性。对于洗涤塔常用的一些改性塑料,其流动性受添加剂、填充物等因素影响较***。
原料干燥程度:如果塑料原料含有水分,在注塑过程中水分会汽化产生气泡,影响熔体的稳定性和流动性,进而导致回流。***别是对于吸湿性较强的塑料,如尼龙等(虽然洗涤塔较少用,但原理相通),干燥处理不当是常见问题。
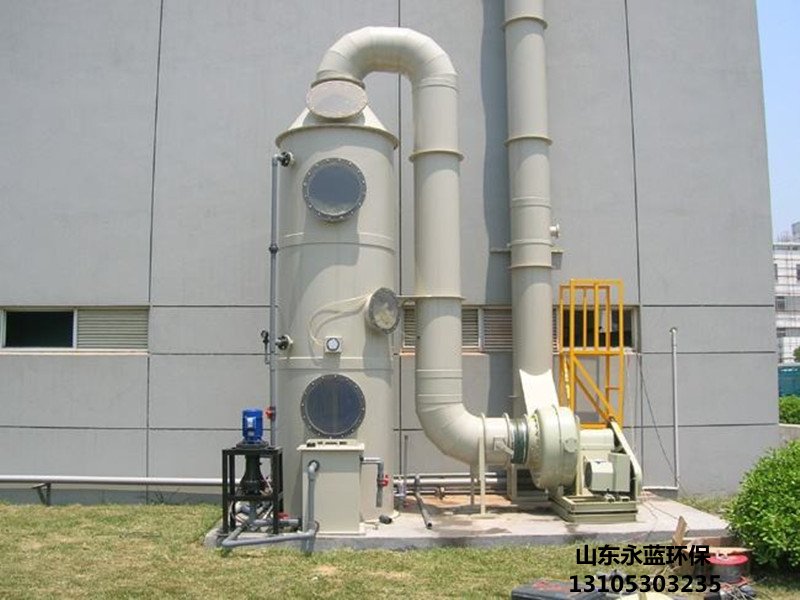
三、回流现象的危害
(一)制品外观缺陷
回流会使洗涤塔制品表面出现缩水痕、飞边、翘曲等缺陷。缩水痕是由于回流区域熔体补充不足,冷却后形成凹陷;飞边则是熔体在回流过程中从模具分型面或其他间隙挤出所致;翘曲可能是回流导致制品内部应力分布不均,在脱模后发生变形。这些外观缺陷不仅影响产品的美观度,还可能降低其在实际使用中的密封性和装配性。
(二)尺寸精度下降
在回流过程中,熔体的流动和重新分布会使制品的尺寸发生变化。对于洗涤塔这类对尺寸精度要求较高的设备部件,尺寸偏差可能导致无法与其他部件准确装配,影响整个设备的性能。例如,填料支撑的尺寸不准确可能使填料安装不均匀,降低洗涤塔的废气处理效率。
(三)内部质量隐患
回流会在制品内部产生应力集中区域,削弱制品的强度和韧性。在使用过程中,这些应力集中部位容易成为裂纹源,使洗涤塔部件在承受一定载荷(如气体压力、振动等)时发生破裂,缩短产品的使用寿命,甚至可能引发安全事故。
四、防止回流的措施
(一)模具***化
1. 温度控制
采用精准的模具温度控制系统,如热电偶测温与分区控温技术,确保模具各部位温度均匀且稳定。对于***型洗涤塔模具,可增加冷却通道的数量和布局合理性,提高冷却效率,减少温度差异。例如,在厚壁部位设置更多的冷却管道,加速热量散发。
在注塑前对模具进行预热,使模具达到适宜的初始温度,避免熔体与冷模接触产生过***的温度梯度。预热温度应根据塑料原料的***性和制品结构来确定,一般控制在塑料的玻璃化转变温度以上、熔点以下。
2. 排气设计
在模具设计时,合理设置排气槽和排气孔。排气槽可沿模具分型面、型芯与型腔的配合面等位置开设,深度和宽度根据塑料原料和制品结构而定。对于洗涤塔上复杂的结构部件,可在容易出现困气的部位,如肋条、凸起处等,增加额外的排气孔。
采用透气性******的脱模剂,有助于在注塑过程中排出模具内的空气,同时减少熔体与模具之间的粘附力,降低回流风险。
3. 结构改进
***化流道设计,采用圆形或梯形等截面形状规则、光滑的流道,减少熔体流动阻力。合理确定浇口的位置、数量和形状,使熔体能够均匀地填充型腔。例如,对于对称性较***的洗涤塔部件,可采用中心浇口或多点浇口,保证熔体在各个方向上的流动平衡。
对模具进行抛光处理,提高模具表面的光洁度,减少熔体流动时的摩擦阻力,使熔体流动更加顺畅,降低因流动不畅而产生回流的可能性。
(二)注塑机参数调整
1. 压力控制
根据塑料原料的***性、制品结构和模具结构,通过试验和模拟分析,确定合理的注射压力和保压压力曲线。在注射初期,采用较高的注射压力以确保熔体快速充模,随着充模过程的进行,逐渐降低压力,避免熔体过度冲击模具型腔。在保压阶段,维持适当的压力以补充熔体的冷却收缩,但压力下降幅度要平稳。例如,对于壁厚较***的洗涤塔部件,保压压力应适当提高且保持时间延长。
安装压力传感器和闭环控制系统,实时监测和调整注塑机的压力输出,确保压力的***性和稳定性,有效防止因压力波动引起的回流。
2. 速度调节
根据制品的结构***点和塑料原料的流动性,选择合适的注射速度。对于结构简单、流动性***的塑料原料,可适当提高注射速度,但要避免速度过快产生紊流。对于复杂的洗涤塔部件,如带有多个薄壁结构的零件,应采用较慢的注射速度,保证熔体平稳充模。一般可通过注塑机的多级注射速度控制功能,在不同充模阶段设置不同的速度值。
结合注射速度的调整,***化注塑机的螺杆转速。螺杆转速影响塑料原料的塑化质量和输送效率,合适的螺杆转速能确保熔体以均匀的速度和质量注入模具型腔,减少回流倾向。
3. 温度管理
***控制注塑机的料筒温度、喷嘴温度和模具温度。料筒温度应根据塑料原料的熔点和加工范围进行设置,一般分为几段控温,从加料口到喷嘴温度逐渐升高,以保证塑料原料充分塑化且具有******的流动性。喷嘴温度要略高于料筒温度,防止熔体在喷嘴处凝固堵塞。同时,密切关注模具温度的变化,通过模具温度控制系统将其稳定在适宜的范围内,避免因温度波动导致回流。
在注塑过程中,定期检查和校准温度控制系统的准确性,确保温度传感器和加热装置正常工作。对于一些对温度敏感的塑料原料,可配备高精度的温度测量仪器,如红外测温仪等,实时监测熔体温度和模具温度。
(三)塑料原料处理
1. 干燥处理
根据塑料原料的吸湿性,选择合适的干燥方法和设备。对于吸湿性较强的塑料,如聚酰胺(PA)等,可采用高温烘干箱进行干燥处理,干燥温度一般在 80 100℃,干燥时间根据原料的含水量和厚度而定,通常为 2 4 小时。对于吸湿性相对较弱的塑料,如聚丙烯(PP),可采用除湿干燥机进行干燥,将干燥后的原料水分含量控制在较低水平,一般小于 0.02%。
在注塑前,对干燥后的塑料原料进行密封包装,防止在空气中再次吸湿。同时,尽量缩短干燥后的原料在空气中的暴露时间,及时进行注塑成型操作。
2. 原料选择与预处理
***先选择流动性***、分子量分布均匀的塑料原料,这些原料在注塑过程中能够更***地填充型腔,减少回流的可能性。对于一些需要改性的塑料原料,如添加填充剂、增韧剂等的塑料,要严格控制添加剂的含量和分散性,避免因添加剂团聚或分布不均影响熔体的流动性和稳定性。
在注塑前,对塑料原料进行充分的预热和干燥处理后,可进行预塑化操作,即将原料在料筒中经过螺杆的搅拌和加热,使其达到更***的塑化状态,进一步提高熔体的质量稳定性,降低回流风险。
五、结论
洗涤塔注塑成型过程中的回流现象是一个复杂的工艺问题,涉及模具结构、注塑机参数设置和塑料原料***性等多个方面。通过深入理解回流产生的原因和危害,并采取针对性的防治措施,如***化模具设计、***控制注塑机参数以及妥善处理塑料原料等,可以有效地防止回流现象的发生,提高洗涤塔塑料制品的质量和生产效率。在实际生产中,需要综合考虑各种因素,不断进行试验和***化,以实现***的注塑成型效果,满足洗涤塔设备对塑料部件的高性能要求。